The Production Process of Rubber Sheets
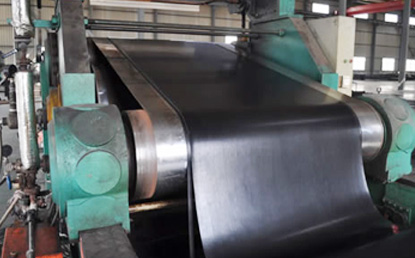
Different rubber products have different processing processes. Formulation, rubber mixing, calendering, extrusion, molding and vulcanization are the basic processes for the production of rubber products.
According to the performance requirements and manufacturing process conditions, the formula of rubber sheet is tested, practiced, identified, and the raw materials are reasonably selected to determine the dosage and ratio of various materials. Under the premise of not reducing product quality, reduce the cost of rubber compound, increase labor productivity, reduce energy consumption in processing and manufacturing, and improve production efficiency.
The mixing is the first step in the production process of rubber sheet. Its task is to mix the raw rubber which is required by formula and various raw materials to make the rubber compound which meets the performance requirements. That includes two main processes – Plastication Process and Compounding Process. Compounding processing is based on Plastication Process. The two processes are commonly known as rubber mixing processes. The rubber mixing equipments mainly have open mill and internal mixer.
Calendering of rubber sheet is to make rubber compound into a sleek sheet which has a specified section thickness and width through the use of calender. Sheets which have large section thickness can be separately calendered into thinner sheets and then laminated to the sheets with specified thickness.
The final step in the production of rubber sheets is vulcanization. The macroscopic characteristics and microstructure of rubber products have changed during this process. The temperature, pressure and time during vulcanization are the main factors to constitute the vulcanization conditions, and are also called three elements of vulcanization.
